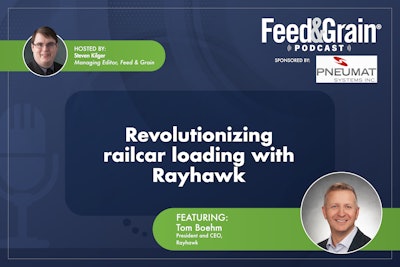
In this podcast, host Steven Kilger, is joined by Tom Boehm, president and CEO of Rayhawk, a pioneering company that's transforming the grain handling industry with its innovative automated rail loading system. This new technology ensures no employees need to be on top of railcars during the loading process, enhancing safety, efficiency, and overall job satisfaction.
Steven Kilger - 00:00
Hi Everyone! My name is Steven Kilger, I’m the Managing Editor for Feed & Grain Magazine and the host of the Feed Grain Podcast. Thank you so much for joining me today as we dive deep into the issues affecting Feed Manufacturing, Grain Handling, and allied industries.
Today’s episode is brought to you by The BinWhip from Pneumat Systems. The powerful Dual Impact BinWhip removes the toughest buildup and blockages in industrial storage silos – without hazardous silo entry. Learn more today at binwhip.com.
In today’s episode, my guest is Tom Boehm, president and CEO of Rayhawk.
Rayhawk is an exciting new company that just kind of entered the industry. It designed a system to completely automate the rail loading process at grain elevators. Analyzing and looking at latches to see if they're damaged or if they're in a different position than normal. This means that no employees have to be on top of railcars during loading, improving safety, efficiency, and hopefully the job satisfaction of your team.
I hope you enjoyed the interview. If you want to help out with the podcast and are listening to this in a podcasting app, please rate us and subscribe.
If you're listening online, sign up for the Feeding Grain newsletter, Industry Watch, to see all the latest podcasts and stay up to date with the latest news from around the industry. Now on to the show.
Kilger - 01:13
Thank you so much for joining me today. So for any listeners out there who might not be aware of what you and Rayhawk do, you mind telling us a little more about yourself and what you kind of do in the industry?
Tom Boehm - 01:24
Thanks a lot for having me here today, Steven. I'd be very happy to talk to you a little bit more about Rayhawk technologies and explain the wonderful technology that we've created. Now what we've done is we've taken the latest in technology that's available in hardware and software and we've worked together to create an autonomous solution to open and close top-filled granular style railcars.
Now what this technology does is it allows us to remove the human being off of the top of the railcar. Now for decades, human beings have been on top of railcars, bending over, opening latches, and tied off using the latest fall protection systems But again, they're still working in the elements, they're working in the wind and the rain, and in some conditions the snow.
And there's hazards, there's lower back strains, there's slips and trips, there's twisted ankles. You're working up at a height that isn't a great place to be and thankfully with today's technology, with what we've done with it, with the wonderful people we have working for us, we've been able to create a solution that's been able to remove the need to have that human being in harm's way on top of a railcar.
Kilger - 02:28
Yeah, I mean. And I think for safety at feed mills, at grain elevators, any of these kinds of big agricultural places, the focus is always on engulfments and things like that. But the loading of rail cars, that's got to be a huge amount of just the day-to-day injuries that people have.
I mean, it's a monotonous task that you're doing. And over again, mistakes get made.
So the ability to kind of automate it, it's not only going to, it seems like it's going to save people so much time. It's going to save them so much money.
It's got to be able to make their employees so much safety and free them up to do so many other things. And hopefully, we can get away from this grind that we have at grain elevators, you know, where people are expected to kind of come in when the rail comes in and that's what we focus everything around. So, it's a fantastic idea.
What inspired you guys to develop this kind of Rayhawk system? How has it evolved? Because when you showed it off at GEAPS this year, I mean, you talked on the trade show, at least those first couple of days. I tried to get to your booth, and I had a really hard time getting over there.
Boehm - 03:27
We were very, very pleased with the response of the community, of the agricultural community at GEAPS this year. It was just such a wonderful experience. You know, two years ago in 2022, I traveled down to the GEAPS event in Kansas, GEAPS Exchange. And I was just so impressed with the hospitality of the other exhibitors, the people that attended that show.
It was just a warm climate, and everybody was more than happy to have a great conversation and help build. So that paved the way for us to want to be there this year. And are we ever happy that we did?
To point out the attendance at the booth, the feedback we got from the industry, as far as, you know, yes, these are known issues. This is arguably the issue that nobody wants to talk about because There has never been a solution and now that there is the excitement and the lineup of people that were at our booth almost non-stop is a testament to that.
The industry is excited to see finally there's a solution here where we can get around this. So when you talk about safety, it's easy to see. You know you have people working at heights and you're walking, you're jumping from car to car, rail car to rail car, and yes you're tied off to a fall restraint system above. But that doesn't make it any better if you slip and fall either inside the car or out of the car. You could be hanging there for a while until somebody can come and rescue you because when you're in fall restraint you can't self-rescue.
There's no ability to somehow grab the binder, tie it to your back, and pull yourself up.
So it does require other people to intervene and hanging in a five-point harness is not good for you either. There are many medical professionals out there who can tell you the dangers of hanging in a suspended mode like that. And that's all while considering that you didn't hurt yourself when you fell.
We've heard stories where people slip and fall off the rail car and they get a bit of a pendulum effect, and they smash into the side of the rail car, or they hit something else on the way down. And this could be bumps and bruises, it could be broken bones, or it could even potentially be a fatality. None of them are great.
You know when we look at what's going on in the industry and we look at what we're capable of as human beings and how technology has been growing and at an increasing rate around us, why are we not taking our people and doing more meaningful activities and automating the ones that potentially create safety risks or business risks?
And that can be automated and that's really what this is about now is that we now have somebody available to pull it into a more meaningful role at the same facility to help increase production, to help keep other areas of the plant, the facility running that may or may not be shut down to allow somebody to be freed up to go load railcars. This is progress, this is an evolution in the industry. And you know, it means so many more things. The safety piece is just one of those pieces along the way.
It's like, yes, we want people to come to work and go home in that same condition. And we want people to feel good about working for the companies that we work for. We want people to feel that they're working for not just a progressive company, but for companies that have their safety and their well-being at the top of mind. At the end of the day, we all compete globally and our agricultural customers and our mining customers are no different. They have to be competitive at that top level, best in class, lowest cost per ton and this is a huge stepping stone for them towards that.
Kilger - 06:37
Yeah, especially since the way the industry runs and has had one for a long time is when train cars come in it is an all-hands-on-deck situation and if you have to work a 16-hour day to get it loaded and out the door because you only have a limited amount of time, that's what you do. One of the biggest things workers these days ask for, and in an industry where people are trying to recruit nonstop because we can't find workers, is that kind of quality of life. I mean, plus who wants to sit out there and load a rail car in rain and sleet and snow on top of there? And no one wants to do that. We all want to be the guy in the booth checking over things and making sure it's all going to plan.
Boehm - 07:19
That's very well said and you know we might also add that in agriculture, I grew up on a farm and in a family operation I was quite involved until I was probably my mid-30s and you know so I spent my fair share of time in a combine and all in grain and so on and it's been a few years now and have things ever changed.
I still am very connected with the farming industry and a lot of friends I grew up with are still farming When it's time to harvest, it's time to harvest and you cannot have anything holding you back and that includes the grain elevators. They need to be able to receive, they need to be able to ship because they've only got so much volume that they can carry as well. And when it comes down to when the rail companies drop off the rail cars, you've got to be able to load. They've got to schedule and maintain.
This is not the amount of leeway in the entire supply chain of taking crops off the field and delivering them to the end facility where they're crushing it and turning it into flour or if you're export market, whatever it may be, that is such a fine balance now that everything must always keep moving.
And if there's a way that railcars could be dropped off, And you can have minimal delays before you can start voting, you know, less reliance on humans to show up to facilitate that process. Then it gives you a little bit of freedom on the business side and on the facility operations side to say, you know what, it's okay that the real company dropped off a unit train and an unplanned or unexpected schedule.
We can start voting. We've got the facility, we've got the people, we've got the technology that we don't have to have a small contingent of people. To come there to get it going, maybe just the operator has to be dispatched, right?
Kilger - 08:56
Yeah, and as conveying speeds have increased so much in recent years, this gives operators options, right? Because it's only so fast you have your rail cars being loaded.
If you're using people with automation, you're able to, I mean, I know the process takes a little while, but you're able to up that efficiency and get more rail cars through faster. We know that it's a great invention.
I think it's going to solve a lot of issues. That's why, you know, you guys were swarmed to teams. How does it work? How does it integrate the vision eyes to do things? How does it automate it? What exactly is the process that a real car goes through?
Boehm - 09:32
It's almost a bit futuristic. I mean, for years, maybe decades, you know, we've been watching our movies and our blockbuster hits that have utilized facial recognition and digital technology to recognize things. And you know, that's here, it's now.
The technology that's available with cameras and so on is that it's allowed us to Train the computer to understand what a real car looks like, what a latch looks like, what a lid looks like, and by overlaying that with a lot of programming, We've been able to develop something that's mechanically simple and very computer complex.
So envision this. The Rayhawk system replicates very similarly to what you would consider a gantry-style overhead crane if you will. For those that are familiar with industrial workplaces, this would be quite common, but it's made up of legs and long-running rails and in a bridge that rolls along those rails and in a tool body that moves back and forth along that bridge.
The camera system is mounted to the system. So as the railcar comes into view of the cameras, the camera can right away identify, hey, is that a railcar? Is that a top-loading railcar? Does that have this particular style of lid or latch on it?
As soon as it recognizes what's coming into its operating window, It can then start to make decisions to go, okay, is the rail car, is the lid closed, is the latch closed, is the lid open or is the latch open? Is it coming in backwards or is it coming in forwards?
Once it's able to make those decisions then it can give the computers other further instructions to say, okay, now we need to open this rail car because further behind us it wants to go into the filling circuit so we need to make sure that every latch is opened before the lid is opened. But then we want to make sure all the lids are open And we want to make sure that the railcar is clean inside so we want to scan the inside of the car and make sure that there isn't leftover product from the last shipment or perhaps some contamination in the railcar.
This now readies the railcar to be filled and as it moves past the first Rayhawk stage it goes into the filling circuit where then whatever product is loaded. Once it's full and the operator says, you know what, I've got the required amount of weight or volume inside that railcar, it can then go into the closing circuit. Now in the closing circuit, the opposite set of instructions happens. It identifies the railcar as, hey, it's open, all the latches are open, the lids are open, and the railcar is full.
It can then record any kind of information you may want. Maybe you want a picture of a full railcar, what it looked like when it was full. Then it will go upon closing the lids and closing the latches and even go as far as to seal the latches with a security seal that's required for international shipping standards or to make sure that nobody is tampering with the quality of your goods from point A to point B. And, you know, was it possible to do this, you know, five, ten years ago? I would say not. The technology just wasn't there.
And, but with the advancement in hardware, computerized hardware camera technologies, and so on, we're now able to use this technology We employ a bunch of people that are just brilliant with computer science and programming and engineering and put all this together to create a solution for the industry that allows them to stand back and watch.
This system allows operators to be involved in enabling and disabling or to start and stop the process. But in reality, we don't need an operator there to start and stop the process. This is part of the adoption, the adaptation piece is that we want to make sure that the highest level of confidence is maintained. But in reality, this could be deployed in such a fashion that you could have a centralized control system to help run several facilities at a time if you so choose.
Kilger - 13:19
Yeah, and it seems like it goes beyond what I consider automation. Because automation, when you think about it, it's just like the same process being done over and over again. But this sounds a lot more like what AI is supposed to be used for, right? It's looking at what the situation is and making a decision. It's not just repeating the same actions over and over again, right?
Boehm - 13:40
That's right. When we engage with a client, what we require to do or insist on doing is set up cameras on their industrial site for several months before we get into deployment of the project. And because we're collecting images that are specific to their site, so we can add that to the training database for the cameras. Now you might wonder, okay, well, why do we do that?
Well every once in a while they may get something, a unique situation, and we want to make sure that we capture that. Now a unique situation could be sunlight conditions, it could be dust, it could be shade, it could be rain or snow, or even an odd style of railcar that has not been seen in the fleet. There are still some antiquated pieces of equipment out there in the shipping fleets and a customer may rarely see one of those.
But if they do receive them and they do need to work with them, we want to be prepared. So that's why we capture so much information so that we can continue to train our computer model and make it more intelligent as it goes along.
Kilger - 14:43
People don't think about that. As a human, you can look at a damaged rail car later and be like, oh, that's damaged. But as a computer, you kind of have to train it to recognize what damage could be and why it's important.
Boehm - 14:54
Exactly. Like how much damage is too much damage. I mean we've got decades of experience working with railcars and some of those lids have been frozen down over the years or stuck down depending on the product that they're shipping. You know there's sometimes it can be almost like a heat seal where the product is loaded hot and it's wet and that creates almost a bit of a vacuum on the car and creates that seal to stick. As a result of that, a large amount of operators have used various tools to break the lid free.
Some have resulted in damage to the lids, some damage beyond repair, but I can assure you that all have been bent or damaged even the slightest little bit. So the computer needs to recognize if the lid is ruined? Or is this just user damage over years of opening and closing railcar lids but the railcar lid is still providing the sufficient function of keeping the product contained secure and free of any outside elements?
Kilger - 15:52
Using tools to open up the real card lid is so, I mean, it's a typical thing of why this is so dangerous too, right? Or guys are up on top using these tools. It's dangerous. It just is dangerous work.
What I love about your system is how it makes people more safely. Well, it just takes them out of the equation completely. It gets them off of the thing that is dangerous because there's only so much we can do to mitigate those risks.
Boehm - 16:17
We've learned a lot over the last couple of years talking with customers about, you know, how they're currently opening those stuck lids. And if there's one thing I can say for sure there's been no lack of ingenuity when it comes to how to open a stuck lid. We've seen everything from two-by-fours to crowbars to winches to jacks to pry bars, you name it.
And, but all of them require a certain amount of complexity at times. But more often than not, a physical effort that when you're, if you're standing up 13, 15 feet in the air and you're leveraging something and certain elements are out of your control, one of which is when will that lid pop-free? And if it pops free and you're prying and leaning on some kind of a moment arm to get it to break free, Where's your body weight going? Chances are it's going off the side of the car.
So it's just amazing that more people are not injured by utilizing some of these, you know, makeshift devices to deal just with the problem of stuck lids.
Kilger - 17:20
I mean, people probably do get injured, but it's their minor, right? They're not big enough to get the attention of OSHA or anybody else. So who knows how many people have just moved that tool the wrong way and ended up bruising the side of their arm or, you know, landing on their tailbone on the rail car, damaging that.
Like all those little injuries that never get reported happen all the time around rail cars. So that's why this is kind of, it's cool. And I think that's why the industry is pretty excited about it. Have you guys been installing them in facilities yet? Where are you kind of on the technological pipeline? Are you guys ready?
Boehm - 17:52
We're ready. We are. And we're very proud of the fact that one of our local clients has a real innovation-based mindset. And they were an early doctor of the technology and so they've got it installed in one of their railway systems and they're monitoring it to just assess the success before they take the next steps to move forward with further installations.
And it's statistically we track this, we have dashboarding and so on that we're monitoring quite closely and it's just a tremendous success. So we're quite happy with that. Where we're at in the commercialization of the product is that we utilize the GEAPS exchange in 2024 as our launch point. We went down and hosted an idea exchange program and presented there and then hosted an exhibit that was, you know, as we spoke about earlier, very, very successful. And now there's just a lot of conversations going on.
We're working with quite a few clients on what it means to their business, what sites would they like to start with, and where and why. Are these historic sites that have had higher injury rates or the key locations within their shipping network? Why this particular location versus the next and the same time it's allowed us to learn more about their business as well as why they make certain decisions on safety. What are the primary drivers that are leading them towards this technology today and in a future mindset of where they want to be years down the road?
Kilger - 19:15
Yeah, I mean, and I'm sure you're kind of at that stage where there's a lot of excitement and a lot of conversations going off. It's exciting though. I mean, it must be after all these years of development to finally be ready to send these out the door.
Boehm - 19:27
Yeah, it's you know the one thing that I can repeat I guess if you will and that is it was just a resounding message time and time again from the customer base that there has not been one customer or potential user come to us, and had their doubts about this technology's place in the industry.
Every one of them said this will be a common mainstay technology in our industry over the next few years. There's no question of if this will be applied. It is, who's going to buy it first? How far are they going to go with it? And how many are they going to install in the initial orders?
Yeah, well, it solves so many common problems. I mean, that we've talked about. Inefficiencies at the mill, safety concerns for workers, and worker shortages. It's just kind of one of those solutions that Once you present it, everyone in the room just goes, well, yeah, obviously, we should be doing this.
You know, I grew up in rural Saskatchewan and growing up, I won't say how many years ago, but you know everybody knew somebody that voted rail cars. In fact, at one point in time, going through high school and so on, that was one of the most desirable jobs because typically the grain companies paid a little bit more money than what you would get pumping gas or changing tires at the local service shop or in my case throwing bales or whatnot, right? And so it was a desirable job.
But in Today's day and age, it's not a desirable job. Some people want to do that type of work. Aside from all the safety and risk things around it, it's very physical work and it's in less than ideal environments all the time. And we are shipping more products than we ever have before.
Those small town elevators largely those wood crib elevators have all been replaced by, or largely been replaced by, concrete or large corrugated steel facilities that are five times the size to ten times the size of what these traditional little wood crib elevators used to be. The volumes are massive and there's no longer a go-go to railcar and then come in and warm up. It's like, no, you're staying on top of that railcar until we're done because this train's got to go. And that creates other challenges.
Kilger - 21:37
Especially when you're like, oh, by the way, it came in on a Saturday on your weekend too. Sorry, it was supposed to be here Thursday, got here on Saturday. Come on in and work 12 hours.
Boehm - 21:46
Exactly. I joked with them when I was down in GEAPS in Kansas, I'm joking with some guys in the industry who had a little bit of an agricultural background. And I kind of smirked and I said, you know, if people like doing certain jobs, we would have never invented the manure spreader. So. I'll let you fill in the blanks.
Kilger - 22:04
Yeah, yeah. Well, especially in this day and age, I mean, all credit to people that do it now, but it is back-breaking hard labor to the kind of labor that when you are 50 and 60, you start feeling it in your bones and your joints. It's a young man's game, certainly.
Boehm - 22:18
My dad, who, you know, named the company after, cause he had some, he put a lot of years in loading rail cars back when farming got in trouble and we ran into some tough times and some drought conditions and so on in the eighties. We went back to work at the local potash mine and eventually got into building railcars. You know, he put it in perspective that on a unit train throughout a shift, a 12-hour shift, you could be bending over as many as 1,500 times to touch your toes. And when you think that you're bundled up, you're maybe wearing, you know, Insulated clothing because it's cold and whatnot.
And you've got a fall arrest system on you that acts a lot like a seat belt. Sometimes if you're going over rough roads it locks up once in a while and it's always kind of gently pulling back at you because you're on a retractable lanyard. Bending over that many times in a shift can be quite something.
Not to mention every time you're bending over you're doing something. You're lifting a weight, you're pushing a lever, you're doing some kind of a manual or mechanical movement with your hands. And on top of that, you know, you're cold or maybe you're not feeling you're at your best. You've got slips and trips hazard, you're working at heights, so maybe you're a little bit nervous.
And then you do this repeatedly day after day after day, you start to paint a picture that this is a less-than-ideal experience. And you know, what kind of joke how maybe our human workforce isn't as tough as it used to be. I'll say one thing, we're smarter than we used to be because we've learned more.
We've seen the way things, where injuries happen, we see how we can improve things along the way and we create safer, more progressive work environments. I think that the antiquation of having people on top of real cars is just another one of those steps forward in the industrial world that we're going to use the latest technology and we're going to be able to put people in a better position and by doing so we're going to be able to put our operations and our companies in a better position as well.
Kilger - 24:11
Okay, definitely. Well, for anyone who wants more information, where should they find you? Where should they get more?
Boehm - 24:17
Well, you know what, we have a tremendous team here, some of which are doing a lot of great work on the marketing front as well, so you can find us on YouTube, of course, you can find us on our webpage www.rayhawk.ca and just reach out, just get connected, whether it be LinkedIn, YouTube, direct to our website, we'd be more than happy to have a conversation with you to explain a little bit more about technology and increase your level of understanding.
Kilger - 24:42
Yeah, make sure to do that. And I hope that you guys reach out with any further developments to us. If you're great, we'd love to talk to you again, and hopefully, we can visit one of the facilities that install one of these things so we can see it. Well, thank you so much for talking to me today.
Everyone out there listening, thank you so much for doing that. Until next time, stay safe.